SEMICON Europa ist mittlerweile eines der größten europäischen Events der Elektronikindustrie: Werden wir Sie dort sehen? Read now in German, or below in English.
SEMICON Europa wird bereits zum zweiten Mal zusammen mit der Productronica bzw. Electronica auf dem Münchener Messegelände veranstaltet. Wir bei Cimetrix freuen uns, wieder – gemeinsam mit anderen in der Halbleiterindustrie – in der SEMICON Europa Halle auszustellen.
Nach einigen Jahren schwindenden Besucheraufkommens, wirkte die Veranstaltung im vergangenen Jahr deutlich wiederbelebt. Wir hoffen, dass wir diese Begeisterung auf der Show 2018 erneut erleben werden. SEMICON zieht traditionell ein einflussreiches Publikum aus allen Bereichen der Mikroelektronikindustrie an, und kombiniert mit einer zweiten Messe (Electronica) am selben Standort, wird sie zu einer der größten globalen Elektronikmessen. Dementsprechend gehen wir davon aus, dass SEMI auf der von SEMICON West geschaffenen Dynamik aufbauen wird, um führende Unternehmen aus der gesamten Lieferkette für die Produktion zu erreichen, da der Schwerpunkt auf Smart Manufacturing weiterwächst.
Während dieser 4-tägigen Messe werden wir SEMI Board Meetings, SEMI Standards Meetings, Smart Manufacturing Sessions und vieles mehr erleben. Alan Weber, unser Vizepräsident für Neue Produktinnovationen, wird am Mittwoch, den 14. November, von 11:00 - 111:15 Uhr auf einer dieser Sitzungen in der TechLOUNGE (Show Floor Hall A4) "Making Smart Manufacturing Work" vorstellen. Unser Team freut sich, mit Kunden, Interessenten und Kollegen zusammenzutreffen und neue Möglichkeiten zu diskutieren.
Wenn Sie mehr darüber erfahren möchten, wie Cimetrix-Produkte bei Ihren Smart-Manufacturing-Zielen helfen können, besuchen Sie unseren Stand A4635 während der Messe. Sie können jederzeit einen Termin auf unserer Events-Seite vereinbaren. Wir freuen uns darauf, Sie dort zu sehen!
SEMICON Europa is now in its second year as a co-located event with either Productronica or Electronica in the Messe München exposition center in Munich, Germany. Cimetrix is pleased to once again be exhibiting in the SEMICON Europa hall with others in the semiconductor industry.
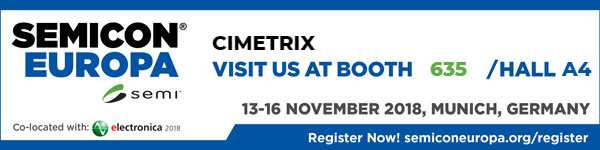
After several years of dwindling attendance, this event felt distinctly revitalized last year, and we hope to see that excitement once again at the 2018 show. SEMICON traditionally attracts an influential audience from every sector of the microelectronics industry, and with a second trade fair (Electronica) at the same site, it is becoming one of the largest global electronics shows. Accordingly, we fully anticipate that SEMI will build on the momentum it established at SEMICON West to bring in leaders from the entire manufacturing supply chain as the emphasis on Smart Manufacturing continues to grow.
During this 4-day trade fair, we'll see SEMI board meetings, SEMI Standards meetings, Smart Manufacturing sessions and so much more. Alan Weber, our VP of New Product Innovations, will present “Making Smart Manufacturing Work” at one of these sessions in the TechLOUNGE (Show Floor Hall A4) on Wednesday, November 14, from 11:00 – 111:15. Our team is excited to participate, to meet with clients, prospects, and colleagues, and to discuss new opportunities.
If you would like to learn more about how Cimetrix products can help with your Smart Manufacturing goals, please stop by our booth A4635 during the show. You can also request a meeting any time on our Events page. We look forward to seeing you there!