In the introduction to this series posted December 19, 2017, we listed some of the manufacturing stakeholders whose work objectives are directly addressed by the applications we’ll highlight in subsequent postings. Before getting into the specific capabilities and benefits of these applications, however, it seemed appropriate and timely to share a little bit about the process that the leading EDA practitioners use to ensure the equipment they are purchasing will support these applications. “Appropriate” because you may need to review and update your own purchasing specifications to clearly convey your requirements in the areas that are not directly covered by the standards (like model content, performance, and stability); “timely” because we at Cimetrix have recently conducted a number of customer workshops and seminars in which this process was effectively used and refined.
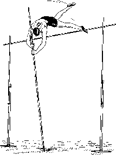
In particular, this article explains how the careabouts of key stakeholder groups are “translated” into specific EDA interface requirements which can then be directly included in the purchasing specifications. As more semiconductor manufacturing companies take this approach, effectively “raising the bar” for the entire industry, the collective capability of our equipment suppliers will increase in response, to everyone’s benefit.
In the previous post, we suggested that manufacturing stakeholders, KPIs, applications, and equipment data are all interrelated. Since the ultimate beneficiaries in this value chain are the stakeholders themselves, the challenge then becomes how to capture their requirements effectively… because these are busy people whose time is precious. Through a number of interviews with leading manufacturers over the past 18 months, we discovered that the best way to accomplish this is through a focused, interactive questionnaire process. By asking very specific questions about people’s daily tasks, problem areas, expectations, success criteria, and other items of constant concern, we can take a generic EDA purchase specification outline and generate a complete, factory-specific set of EDA purchase specifications in a matter of days. This is time well-spent when you consider the value and volume of equipment potentially affected… and the opportunity cost of not having these requirements clearly expressed.
The stakeholder answers to the questionnaire serve a broader purpose as well, because in addition to driving the content of the equipment purchase specifications, they also form the basis for a lot of manufacturing technology development within the factory. This overall process is shown in the figure below; documents and related artifacts are shown in red; the affected organizations (of which there are many!) are shown in blue.
A blog posting can only hope cover a fraction of this overall process, but the sample questions below should give you an idea of how it works.
Sample questions for the Manufacturing Automation and Technology Development stakeholders include:
- Are you familiar with SEMI E157 (Module Process Tracking)? Is it implemented on any of your current tools, and if so, do you monitor those events?
Do you require that all state machines, states, state transition events, and attributes of the objects defined in the referenced 300mm SEMI Standards be implemented? If not, why not?
- Do you currently use information from sub-fab systems in any of your on-line production applications, like FDC, PHM, R2R control, or others? If so, what range of equipment is supported, and how (pumps, chillers, abatement systems …)?
- How do you express performance expectations for process variable reporting, such as sampling frequency, # parameters per chamber, report sizes, total bandwidth of all data reported, maximum latency of event generation, etc.?
Sample questions for Production Operations and Engineering Support people include:
- How do you schedule carrier pick-up and delivery from/to equipment, respectively? Is this done using algorithms in the AMHS/MCS/OHT system components, or do you get real-time updates from the equipment about pending lot completion and tool availability?
- Do you need to have remote access capability for checking basic tool status outside the fab?
- Do you require your suppliers to provide built-in data collection schemes (pre-defined reports, macros, etc.) to support common monitoring, maintenance, or diagnostic processes?
- Do you have a list of parameters/events that must be collectable to support your production application portfolio?
- Do you monitor any of the low-level actuator/sensor signals in the various mechanisms that make up a manufacturing tool?
Sample questions for the Procurement and Supplier Relations organizations include:
- What compliance tests/reports do you require of the equipment suppliers before they ship equipment to your factories? Do you ever/sometimes/always visit the supplier's site to observe this process? What about after delivery?
- Do you have a standard supplier response sheet or checklist for your automation requirements? If so, are you satisfied with its clarity, completeness, and ease of use for evaluating responses?
- At what point in the equipment purchasing cycle do you review the capabilities of the interface software (event/parameter lists, model structure/content, projected performance, etc.)? When are these capabilities validated?
- Do you assign a monetary value (say, some % of the equipment purchase price) to the interface software?
If the above discussion triggers the question “I wonder if our EDA purchase specs are sufficient to address the manufacturing challenges we’ll face in the next few years?” give us a call. We’ll be happy to talk about how to support your stakeholders and automation team with an effective on-site workshop to address this question once and for all… It could be the most important next step you take in formulating you own company’s EDA implementation roadmap.
As always, your feedback is welcome, and we look forward to sharing the Smart Manufacturing journey with you.
Click below to learn more about EDA: