A SECS GEM driver can be looked at from a factory or equipment supplier perspective. I will discuss both of them in that order.
Factory Perspective
A little background:
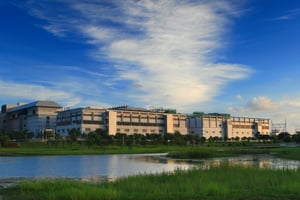
From a factory perspective, a SECS GEM driver is the host software that talks to an equipment’s GEM interface. It allows the factory to take advantage of the features implemented in each equipment’s GEM interface. However, what the factory can do with an equipment’s GEM interface is also limited by what the equipment supplier has included in that interface. The GEM standard is very flexible and scalable, which accounts for the widespread and growing adoption of GEM technology—it can be adapted to any manufacturing equipment and market segment.
It is possible to implement features in a GEM interface. But this also means that just having a GEM interface on the equipment does not ensure that it has been correctly designed to meet the factory’s expectations. An equipment supplier’s poor implementation of GEM can frustrate a factory’s plans for Smart Manufacturing by not providing features that the factory expects that could have been implemented. The tendency of most equipment suppliers is to implement the absolute minimum functionality in a GEM interface to save money. Therefore, it is the responsibility of the factory during equipment acceptance to evaluate the GEM interface to make sure that it is robust and has the full set of required features. The factory must have a clear vision of its needs both initially and later as its Smart Manufacturing goals are realized. It is not unusual for a factory to request an upgrade to an equipment’s GEM interface with more features, but these modifications usually come at a cost.
Although a factory’s SECS GEM driver must be adaptable to different suppliers’ GEM implementations, it only needs to support the specific features that the factory uses. For example, if the factory is only concerned about alarm and event report notification, then it does not need to support the messages for recipe management, remote control or trace data collection. As such, the investment in a SECS GEM driver is proportional to the number of GRM features that are utilized. However, the SECS GEM driver should also support variations in alarm and collection event implementations, because each equipment type will support a unique set of alarms and a unique set of collection events with unique data variable for event reports. Moreover, from equipment type to equipment type, the same collection ID might have different meanings. The SECS GEM driver therefore needs an ability to adapt by having a method to characterize the GEM implementation (such as a list of available collection events) and the ability to map a general capability to the actual implementation (such as “material arrived” = collection event ID 5).
So why would a factory want to use SECS GEM technology?
In order to reach the goals of Industry 4.0 and Smart Manufacturing, factories must be able to monitor and control manufacturing equipment remotely. Therefore the equipment must have a software interface to provide this functionality and the factory must be able to access and use this interface.
Factories could let the equipment suppliers choose their own implementation technologies for this kind of capability, but as a result, different suppliers might take a different approach for every equipment type. This would be tremendously expensive and resource intensive. It is far better to standardize on one or two technologies, and ideally, one that is proven to work and known to have all of the necessary features. This allows the factory to achieve its goals with minimum investment, focusing instead on using the equipment interface in creative ways to improve manufacturing.
SECS GEM is the most proven technology already widely used across the globe and supported by the most sophisticated and automated industry in the world; semiconductor manufacturing. It is also widely adopted several other industries, making it a safe choice. The range of production applications supported by SECS GEM data collection include productivity monitoring, statistical and feedback/feedforward process control, recipe selection and execution tracking, fault detection and classification, predictive maintenance, reliability tracking, and many more. By contrast, alternatives to SECS GEM have so far been demonstrated to be incomplete or immature solutions.
What specifically can you do with the SECS GEM technology?
- Collection Events: Be notified when things happen at the equipment, such as when processing or inspection begins and completes, or when a particular step in a recipe is reached.
- Collection Event Reports: Collect data with collection events. The host chooses what data it wants to receive. For example, track the ID of material arriving and departing from the equipment, or components placed on a board.
- Alarms: Be notified when bad or dangerous things are detected, receive a text description of the alarm condition, and when the issue is cleared.
- Trace Data Collection: Tell the equipment to report status information (software and/or hardware data) at a specific interval. For example, track digital and/or analog sensors during processing at 10 Hz frequency.
- Recipes: Upload, download, delete and select recipes as desired, whether in ASCII or binary formats. Make sure that the right recipe is run at the right time to eliminate misprocessing and minimize scrap. Track when someone changes a recipe.
- Remote Commands: Control the equipment, such as when to start, stop, pause, resume and abort. Custom commands, such as calibrate, skip or anything else can be supported.
- Equipment Constants: Configure and track the equipment configuration settings remotely.
- Terminal Services: Interact with the equipment operator remotely or provide instructions for the operator.
- Extensions: There are numerous extensions to GEM that can be supported but are not yet form requirements. For example, implement wafer or strip maps from E142 to provide and report details about material in XML format.
Equipment Supplier Perspective
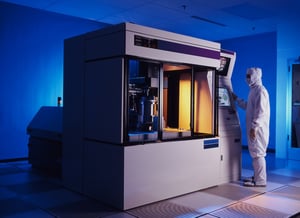
From an equipment supplier’s perspective, a SECS GEM driver is the software used to implement GEM technology on the equipment. In other words, the software to create a GEM interface. The equipment-side software requirements are inherently more complex that the host SECS GEM driver. This is because the equipment-side features are precisely defined by the GEM standard and should be implemented to the fullest extent possible. By contrast, the host can really do whatever it wants, so a limited implementation may be sufficient. In an ideal situation, the equipment supplier will implement just enough features in its GEM interface to satisfy all of its customers and therefore ship an identical GEM interface to all its customers. It is up to the equipment supplier to decide what GEM features to implement and how to adapt them for a particular type of equipment, but the factory should provide clear expectations about its planned use of the interface. It is also the factory’s responsibility to qualify the GEM interface during equipment acceptance. Note that it is not uncommon for factories to withhold partial equipment payment until the GEM interface has also passed its own acceptance.
Some equipment suppliers include the GEM driver as a standard feature on all equipment. This is ideal because it makes the GEM interface much easier to support and distribute. Some equipment suppliers only install GEM when it is specifically purchased. This often results in installation problems because the field technicians may or may not be knowledgeable enough or specifically trained to do this correctly. Other equipment suppliers include the GEM driver on all equipment, but only enable it when the feature has been purchased. This is better than attempting GEM interface installation after equipment delivery because the GEM interface can often be enabled with a simple equipment configuration setting.
Here are some key reasons for implementing a SECS GEM driver:
1. “One ring to rule them all”
By implementing a GEM interface, an equipment supplier can avoid having to implement multiple interfaces. Because GEM is the most feature complete option, the it should be implemented first and Thoroughly integrated with the equipment control and user interface software. If other protocols must be supported, they can usually be mapped onto the GEM capabilities or a separate external system because they only include a subset of GEM functionality.
2. Equipment Supplier Application Software
If the GEM implementation includes support for multiple host connections, then the GEM interface can be used by the equipment supplier itself for many applications. For example, an equipment supplier can develop a software package that monitors and controls their specific equipment at a factory. This can run simultaneously and independently while the factory GEM host software is connected. Many factories are willing to buy applications from the equipment supplier that enhance the productivity of the equipment they have purchased. As an example, equipment suppliers are better equipped to develop predictive maintenance applications that determine when parts are approaching failure and need replacement. These applications can save the factory time and money by avoiding unscheduled downtime. Other applications can also be developed by equipment suppliers to analyze and optimize equipment execution.
3. Competitive Advantage
A well implemented GEM interface can differentiate a supplier’s equipment from that of its competitors. Factories are beginning to recognize the value in controlling and monitoring equipment remotely, and know that a poor GEM interface contributes nothing to a factory’s Smart Manufacturing initiatives. A GEM interface that goes the extra mile to be truly useful empowers the factory to excel at Smart Manufacturing and to be far more productive. Selling equipment in today’s market without a GEM interface is like selling a television without a remote. On the other hand, providing a fully featured GEM interface is like selling a smart television.
Final Words
Experts on GEM technology are available all over world. Because GEM is a mature industry standard and well defined, it can be implemented by anyone in a range of different programming languages and operating systems. however, to save time I recommend using a commercially available product rather than developing the complete GEM interface from scratch. This can save massive amounts of time and effort, and ensures the quality of the resulting implementation.
To speak with a Cimetrix GEM expert, or to find out more about our GEM software products, you can schedule a meeting by clicking the link below.
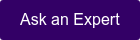