Introduction
In the fast-paced world of semiconductor manufacturing, staying ahead of the curve is important. Industry 4.0 continues to reshape the landscape, and companies in this sector are turning to new technologies and applications to maintain their competitive advantage, improve yield under increasingly stringent process constraints, boost factory and equipment productivity, enhance data collection and information extraction, increase visibility into manufacturing equipment and process behavior, achieve tighter control, and support single-device traceability, just to name a few. In this blog post, we explore how REST APIs enable seamless communication and data exchange with manufacturing equipment, acting as an abstraction layer for the SECS/GEM interface. Furthermore, we highlight the advantages of OpenAPI as the specification language and explain how to quickly discover how an API works.
Industry 4.0 and the Semiconductor Manufacturing Challenge
The semiconductor manufacturing industry has long played a key role in driving technological progress, from consumer electronics to critical components used in aerospace and medical devices. However, this sector is not immune to the challenges of Industry 4.0, characterized by the increasing demand for data-driven decision-making, automation, and connectivity.
Data Extraction
One of the primary challenges in semiconductor manufacturing is dealing with the massive amount of data generated during the production process. This data includes equipment parameters such as temperature, pressure, voltage, and many others critical to ensuring product quality and yield. Extracting, processing, and analyzing this data efficiently is crucial. Traditional approaches have relied on proprietary systems and protocols, leading to compatibility issues and data silos among various stakeholder groups and their respective software solutions.
In contrast, a modern approach incorporating REST APIs that access the capabilities of standard SECS/GEM, GEM300, and EDA interfaces and even custom protocols provides a standardized and well documented means of extracting data from diverse manufacturing equipment and systems. Using REST APIs as the common interface allows data collection from different sources and to different target destinations, paving the way for real-time data analysis and optimization. For instance, the Cimetrix Sapience™ platform employs data collection plan (DCP) templates for gathering data from a potentially wide variety of sources, ensuring consistency and compatibility among them.
Equipment Control
Precise control of manufacturing equipment is essential to achieve high product quality and throughput. Industry 4.0 introduces the concept of smart manufacturing, where equipment is interconnected and can adapt continuously to changing factory conditions. While legacy control systems often lack the flexibility required for today's dynamic manufacturing environment, the modern approach cited above involving REST APIs and multiple underlying protocols facilitates the integration of multiple equipment control systems and the manufacturing applications that orchestrate their interaction.
The integration allows equipment to communicate and coordinate across a process area or the entire factory, enabling real-time adjustments to material dispatch lists, recipe parameter changes, predictive maintenance, and other applications that positively affect manufacturing KPIs (Key Performance Indicators). Again, the Sapience platform provides a uniform environment within which application and equipment interactions are standardized, thereby minimizing the amount of custom software required and ensuring high reliability and performance.
Traceability
Traceability is paramount in semiconductor manufacturing, where precision and accountability are vital. Accurate tracking of every manufactured product component through each process step—including the consumables and durables (fixtures) involved—ensures defects can be traced back to their source(s), and final product quality and safety remain uncompromised. Historically, the approach to traceability relied on error-prone and time-consuming manual record-keeping.
In today’s modern approach, REST APIs, SECS/GEM, and GEM300 enable automated traceability by connecting the equipment from all manufacturing stages into a unified system. Each step in the production process can be logged and traced in real time by multiple applications, including Manufacturing Execution Systems (MES). This ensures that the entire manufacturing flow for a specific device can be reconstructed from the data collected, so there are no gaps in the failure analysis process. A common set of APIs spanning all the SEMI connectivity standards establishes an integrated framework for data exchange among multiple endpoints.
The Advantages of OpenAPI in Software Development
OpenAPI offers several advantages that significantly impact the way software is developed and integrated. It serves as a fundamental building block for modern software development, making it an essential tool for developers and organizations seeking to streamline their REST API design, documentation, and implementation practices. As the need grows for collaboration and multi-language software development, it is an indispensable tool for creating a standardized factory automation workflow.
1. Design-First Approach: OpenAPI allows for the comprehensive definition of an API, including types and examples for every endpoint. A design-first approach involves creating a detailed API definition before writing any code. It serves as an abstraction layer for SECS/GEM, supports specific APIs for each SEMI standard and enables iterative refinement and updates of the API design.
2. Code Generation: OpenAPI offers broad language support for code generation. It generates SDKs in the programming language of choice, facilitating integration with different application architectures (e.g., desktop or web).
3. Powerful Tools: The OpenAPI ecosystem, which includes tools under the Swagger brand, accelerates API learning and experimentation. The Swagger UI provides capabilities to visualize and interact with the API resources without requiring any of the implementation logic to be in place, all based on the OpenAPI specification.
4. RESTful API: RESTful API is a type of web service that uses HTTP methods and URIs to interact with resources, and OpenAPI is the specification for designing and documenting RESTful APIs. This makes it easier to adhere to best practices and ensure consistency and predictability in API interactions.
5. Vast Userbase and Stability: OpenAPI benefits from broad industry adoption and backing by major companies, resulting in a wealth of collective knowledge from building numerous APIs. This robust userbase offers invaluable support for both newcomers and experienced developers.
Hypothetical Case Study: OpenAPI, SECS/GEM, and GEM300 Implementation
Let's look at a hypothetical case study to illustrate the benefits of OpenAPI, SECS/GEM, and GEM300 in semiconductor manufacturing:
Company X, a leading semiconductor manufacturer, faces challenges with data collection, equipment control, and traceability in its production line. To address these challenges, they implement Sapience with OpenAPI, SECS/GEM, and GEM300 across their manufacturing processes.
Once the shop floor is connected to Sapience, developers can start experimenting with the Swagger UI that provides an intuitive and interactive interface to the OpenAPI documentation. For example, looking at the DataCollectionPlan API allows them to quickly understand the options for collecting data at a certain frequency and the format of that request to the equipment.
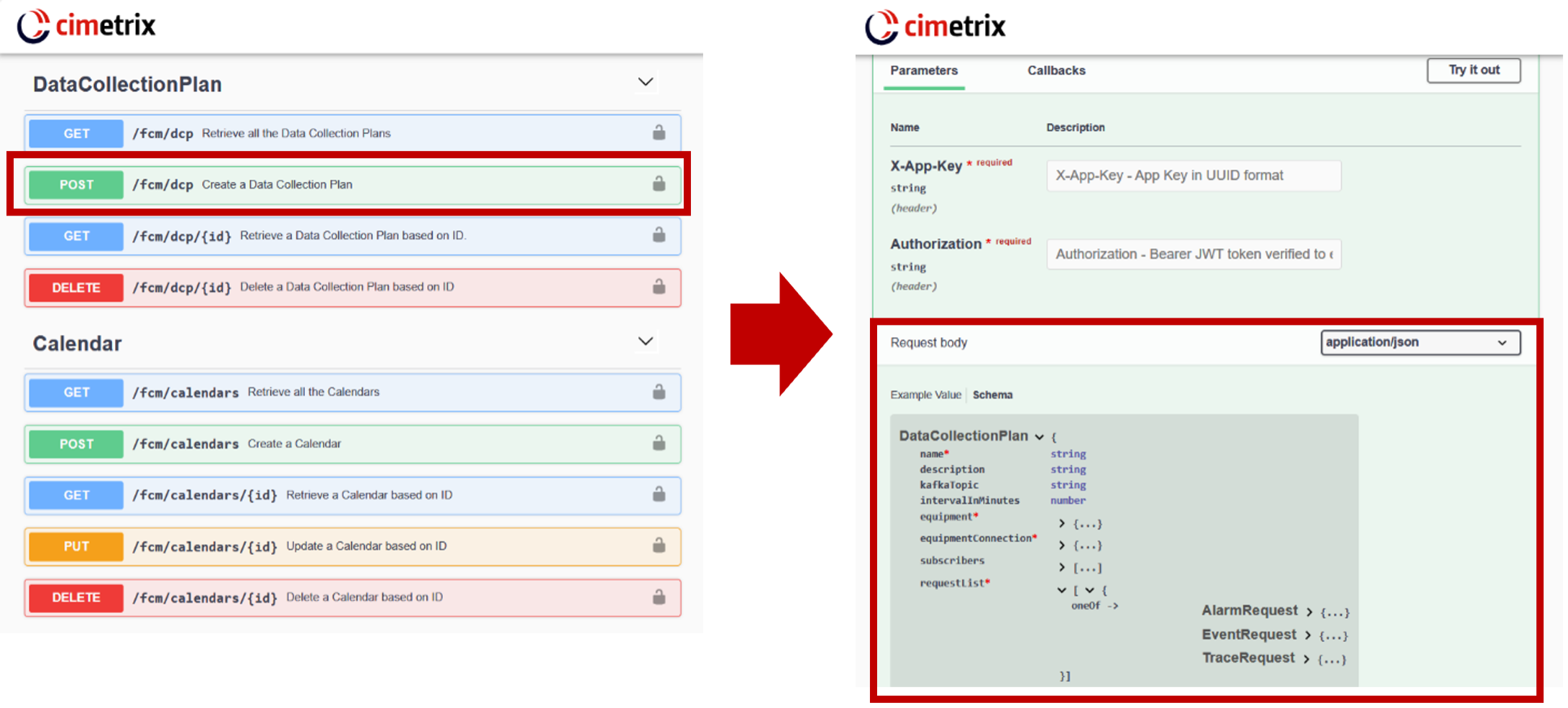
Figure 1 Data Collection Plan API with documentation and schemas
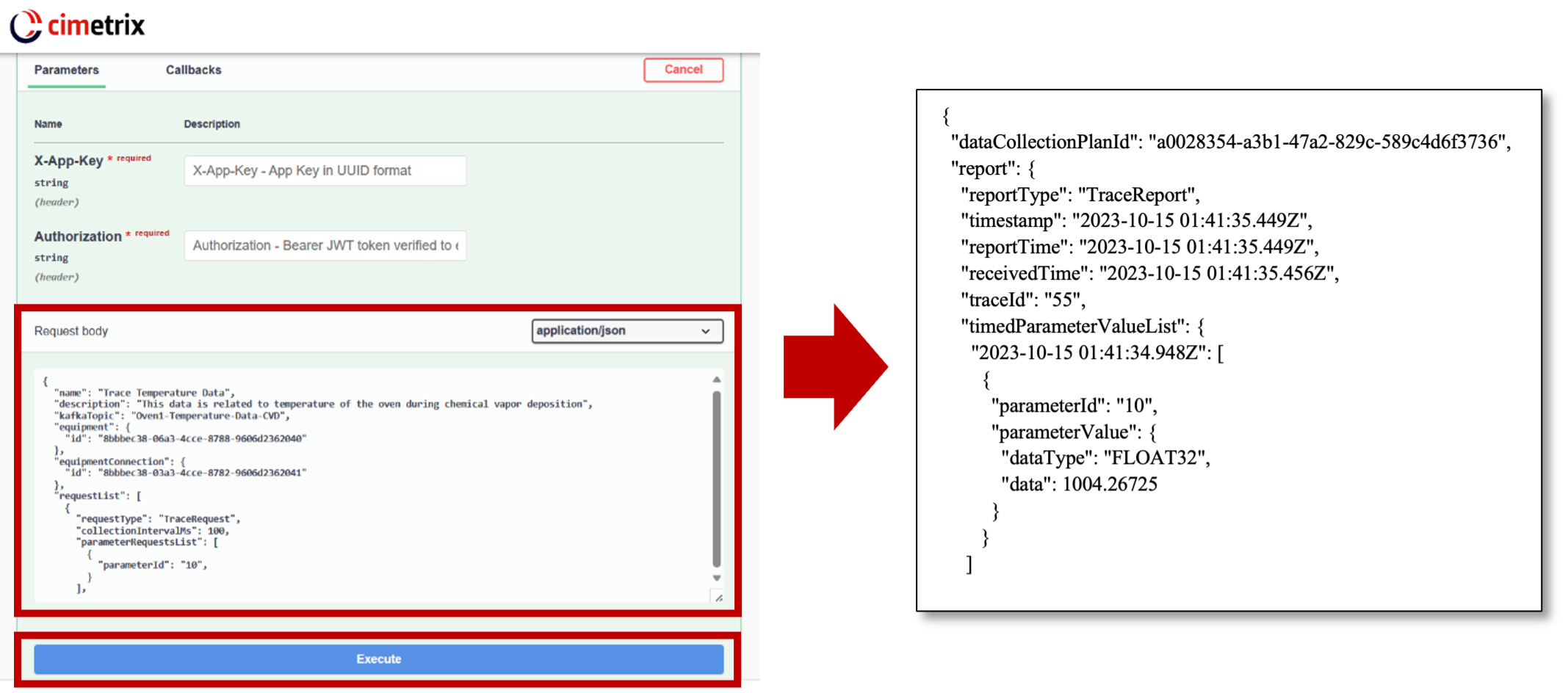
Figure 2 Data Collection Plan API with executable examples and received data
Another important requirement is to control the equipment by selecting the process program, and the SEMI E5 (SECS-II) streams and functions for accomplishing this are well documented and accessible via the Swagger UI. Since the API documentation includes such an example request to the equipment, the learning curve to understand the use of the required remote commands is greatly reduced, so applications prototypes can be built quickly.
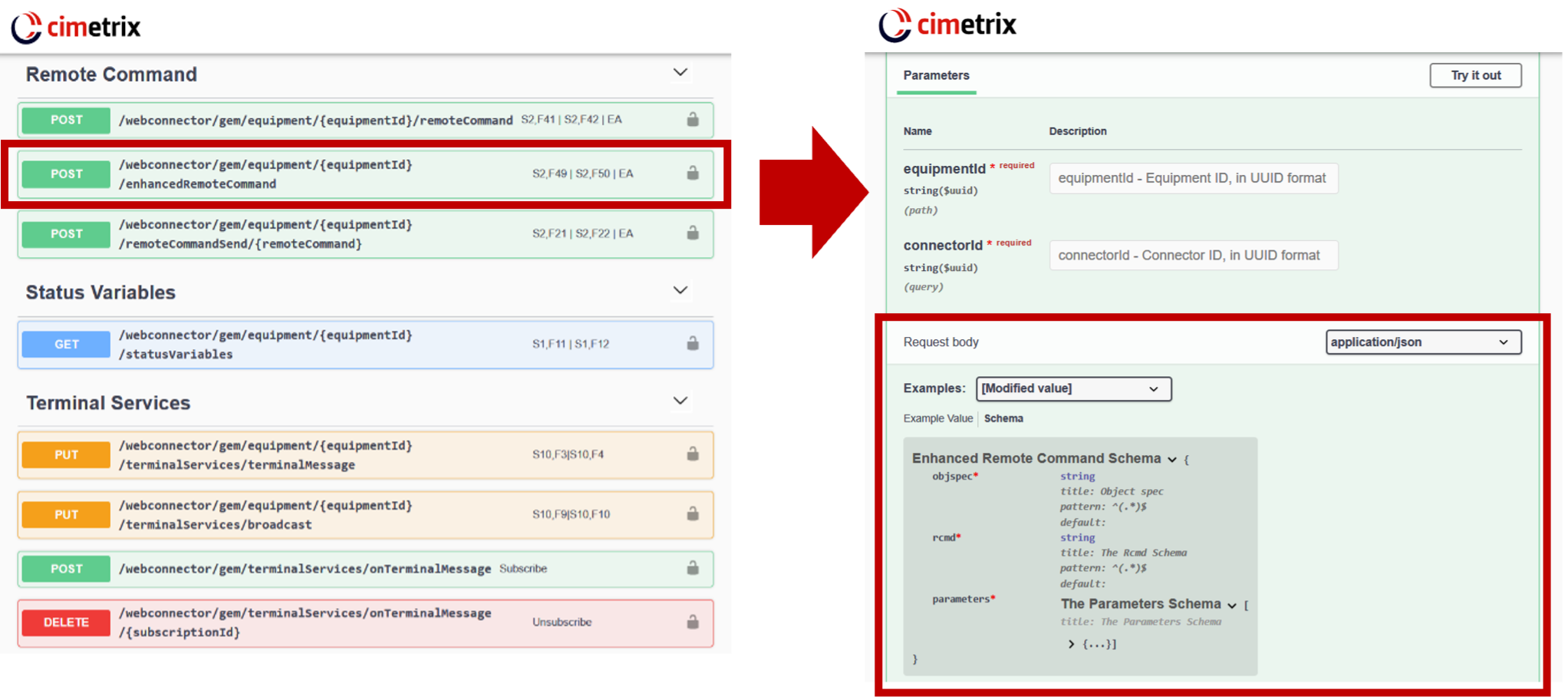
Figure 3 Remote Command API with documentation and schemas
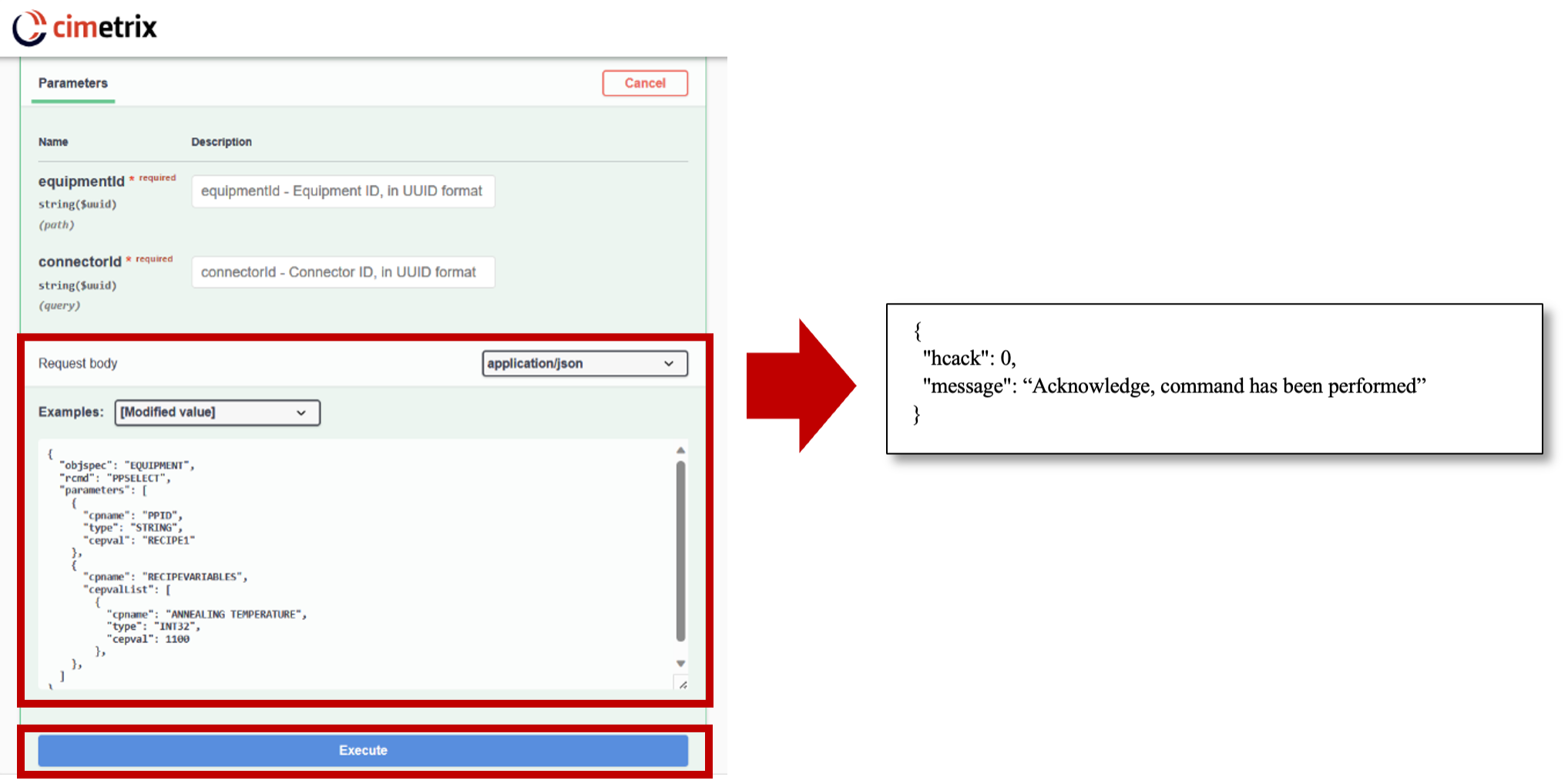
Figure 4 Remote Command API with executable examples and received data
Conclusion
In summary, the REST APIs that serve as an abstraction layer for SECS/GEM constitute a transformative technology for the semiconductor manufacturing industry. They directly address the Industry 4.0 needs of data collection, information extraction, equipment control, and traceability, offering standardized, interoperable, and scalable solutions. Furthermore, companies that embrace the OpenAPI specification powerful associated tools for code generation and documentation are well positioned to thrive in the ever-changing semiconductor manufacturing application landscape, in turn achieving better product quality at higher efficiency and lower cost.
As we move forward, the adoption of solutions such as the Cimetrix Sapience™ platform in semiconductor manufacturing will ensure competitiveness and contribute to innovations that only come with easy access to equipment and process data and the analytical and control applications that consume it. The examples cited above deal with SECS/GEM interfaces, but the Sapience platform also supports other standard protocols such as SEMI EDA (Equipment Data Acquisition) and OPC UA. The same documentation approach has been applied, enabling rapid understanding and use of their respective capabilities.