By David Francis
Product Manager
The creation of a new software product is an exciting process. Often, as was the case with the Cimetrix CIMControlFramework™ (CCF) software, this process begins with a partner that will become the first customer of the product. Cimetrix teamed with Axcelis Technologies to develop a new tool control framework for one of their process tools. A following project with Rorze Automation further developed the framework and produced CCF 2.0. Upon completion of that project, Cimetrix continued the development of the tool control framework to become a standard product that any OEM could use, resulting in the release of CCF 3.0.
The development effort for CCF v3.0 focused on four main areas that improve both the product development capability and the user experience:
- Tighter integration with Cimetrix connectivity products
- Faster data analysis
- Reduced installation time
- Improved training material
1) Tighter integration of CIMControlFramework with factory automation components to implement Interface A and SECS/GEM connectivity
We simplified the data configuration so that parameters, events, and alarms are registered at start up and automatically coordinated with the configuration files for the factory automation products.
In the previous versions, CCF was configured to work with a CIM300 or CIMConnect product that was previously installed and configured for the equipment. The problem was that if someone needed to change the connectivity functionality, that change was not reflected in the tool control portion of CCF, or vice versa. This meant that the required changes had to be implemented twice, resulting in duplication of effort.
Since we wanted to develop the product for a broad range of customers, we wanted to make sure that during tool initialization, OEMs would be able set up alarms, variable definitions, collection events, etc. one time for both tool control by CIMControlFramework and for the connectivity products.
With the tighter integration in CCF 3.0 to coordinate the tool control and the connectivity, initial deployment is now much easier and faster.
Below is an example that shows how alarms, events, and variables are tied together. OEMs create the initial model using EM Developer, and then all of the configured alarms, events, variables are dynamically added to the model after startup. You don’t have to create all the details of the model, just the basic configuration and CCF fills in the data.
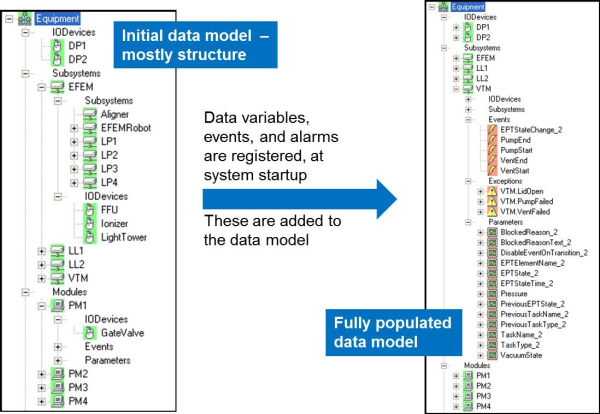
2) Improved User Experience Through Faster Data Analysis
We learned from the initial deployments that tool operators need quick access to process data in order to improve productivity and lower costs. For CCF 3.0, Cimetrix implemented dedicated history tables to improve performance of queries on historical data. The new history tables allow for much faster queries for wafer, EPT and Alarm history information.
All logged information is written to log files. Any log information related to wafer, EPT, or alarm history is also written to the respective table in the on-tool database.
The benefit is fast and easy visualization of the equipment process data that is 20-30 times faster than the previous CIMControlFramework product.
The following graph shows the frequency of alarms reported by the equipment, which can be used to identify problem areas. This type of data now comes back within a few seconds.
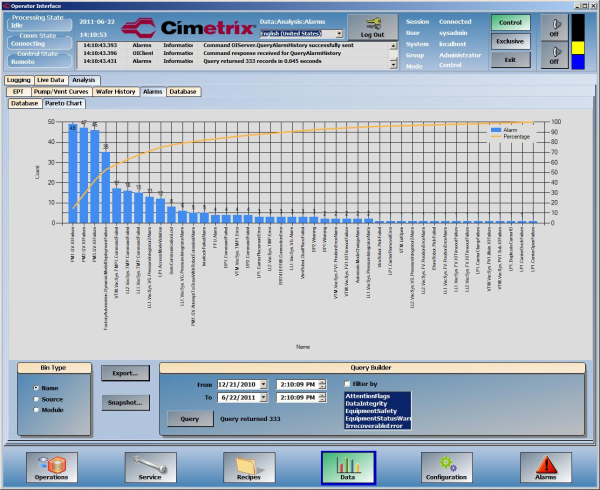
3) Reduce the time and effort of software installation and initial setup
The new installer allows the user to select the specific CCF modules needed and any other embedded Cimetrix products – such as CIMPortal™ or CIM300™ they want to install and configure. The installation is done in 2 phases. The first phase installs all files related to the products selected, including the source code. The second phase installs and pre-configures CCF and any pre-requisite packages. With the installation package, the time to time to install is dramatically reduced.
4) Improved training material and code samples
To help a project team get started faster and get them more productive sooner, the Cimetrix created new labs that offer hands-on exercises. One example is a lab to show the process for customizing user screens. Both the problem case and the completed solution for each lab ship with CCF. The real benefit is customers can use the labs as a starting point for their project or as reference material to help them create their own implementation.
Below is a screen shot from a lab that walks students through the process of creating a custom screen to visualize data for their specific tool, such as visualizing pressures, load locks, robots, load ports, processing chambers, etc.
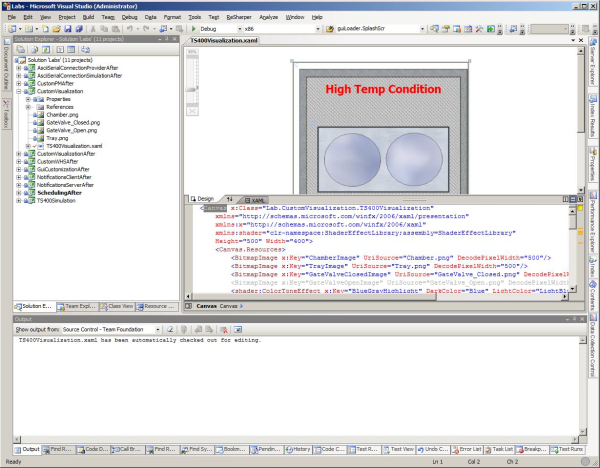
Cimetrix is a software company dedicated to continual product enhancement. This release delivers improved functionality and performance that will benefit our customers. With CIMControlFramework, OEMs have a great solution for tool control that allows them to spend more time and effort on delivering their unique value to the market, and far less time on tool control and connectivity—and it just keeps getting better. This is another example of what Cimetrix does to support our customers to speed them through the development phase and into production.